Originally published October 9, 2023, updated March 7, 2024 by Alyssa Wolfe.
Every link in an ecommerce supply chain supports the entire process. That's why ensuring efficient supply chain management is essential for your ecommerce company’s success. But how do you determine whether your supply chain is performing well — and where you need to improve?
That’s where supply chain monitoring comes in. Let’s take a quick look at the concept of supply chain performance, its significance and the key performance indicators (KPIs) to track. This will help you increase efficiency and get your products to customers faster, ultimately increasing customer satisfaction and profitability.
Why measure supply chain performance?
Effective supply chain management plays a critical role in business success. It lets you understand cost drivers so you can find areas to achieve savings, improve efficiency and exceed customer expectations by reducing delivery time. The best way to optimize your supply chain performance is to measure KPIs and adjust. Analyze key metrics like inventory turnover, transportation costs, warehousing expenses, fulfillment cycle time, on-time delivery, lead time, order accuracy and production cycle time to improve efficiency across your entire supply chain. Measuring these KPIs uncovers inefficiencies and gaps in the supply chain process.
These aren’t just dry metrics — they’re living, breathing numbers that lead directly to increased customer satisfaction. If you measure supply chain performance, you can improve it. If you improve it, customers will get the products they ordered faster, which means more happy customers for you.
KPIs for supply chain performance measurement
Measuring supply chain performance KPIs begins with identifying key metrics aligned with business goals, such as inventory turnover, order fulfillment accuracy and on-time delivery. Start by assessing existing processes and data availability to determine your ability to track each KPI.
Prioritize a select number of KPIs that directly impact strategic objectives and operational efficiency, ensuring they are measurable, relevant and actionable. The frequency of measurement depends on the nature of the KPI and the desired level of insight; some metrics may require daily monitoring, while others can be evaluated weekly or monthly. Start with a few KPIs and expand as you move forward: Beginning with too many can get complicated quickly. Regularly review and analyze KPI data to identify trends, areas for improvement and opportunities for optimization within the supply chain.
On-time delivery rate as a KPI for supply chain performance
The on-time delivery rate refers to the percentage of orders you deliver to customers within the promised timeframe. This KPI holds significant importance because it directly affects customer satisfaction and overall business success. When measuring it’s important to note:
- A high on-time delivery rate ensures customers receive orders on schedule, making them more likely to become repeat customers and recommend your company to others.
- A high on-time delivery rate reflects effective supply chain management and streamlined processes. It indicates that the supply chain is well-organized, from order processing and inventory management to transportation, resulting in efficient operations.
- A strong on-time delivery rate contributes to reduced operating costs. Timely deliveries minimize inventory holding costs, reduce the need for expedited shipping and minimize the risk of stockouts or customer penalties.
By tracking and continuously improving the on-time delivery rate, you can proactively identify areas for optimization, such as route planning, demand forecasting and relationships with suppliers and logistics partners.
Inventory turnover ratio as a KPI for supply chain efficiency
The inventory turnover ratio measures the number of times a business sells and replenishes its inventory within a specific period. You’ll want to know:
- A high inventory turnover ratio indicates the business is managing inventory effectively, reducing the risk of holding excess stock. This leads to cost savings, as it minimizes storage and carrying costs associated with excess inventory.
- A high turnover ratio also indicates effective demand forecasting and inventory management practices. It reflects the ability of the supply chain to accurately anticipate customer demand, preventing stockouts and ensuring timely replenishment.
- A high inventory turnover ratio can improve cash flow. By reducing the amount of capital tied up in inventory, businesses can allocate resources to other areas, such as product development or marketing initiatives. They also enjoy improved customer satisfaction through product availability, ultimately driving up profitability.
Inventory turnover ratio:
Inventory turnover = cost of goods (COG) sold / average value of inventory
Why does the formula use COGS instead of sales? Because businesses typically value inventory at cost. As for average value of inventory, analysts use it to offset the effects of seasonality. They do this by adding the inventory value at the end of one period to the inventory value at the end of the previous period and dividing the result in half.
Example calculation:
- Determine the average inventory level: Add the beginning inventory (at the start of the period) to the ending inventory (at the end of the period), then divide by 2.
Average Inventory = (Beginning Inventory + Ending Inventory) / 2
- Calculate cost of goods sold (COGS): Determine the total cost of goods sold during the period. This includes the cost of purchasing or producing the goods sold during the period.
- Use the formula: Divide the cost of goods sold by the average inventory level.
Inventory Turnover = Cost of Goods Sold / Average Inventory
For example, if a company had $500,000 in COGS and an average inventory of $100,000 during the year, the inventory turnover would be:
Inventory Turnover = $500,000 / $100,000 = 5 times
This means that, on average, the company's inventory was sold and replaced five times during the period. A higher turnover ratio generally indicates better inventory management and efficiency. However, too high and you likely have insufficient stock.
Order accuracy rate as a KPI for supply chain quality
Order accuracy rate measures the quality of supply chain operations. It represents the percentage of orders fulfilled correctly without errors or discrepancies. A high order accuracy rate is indicative of a well-functioning and efficient supply chain. Maintaining a high order accuracy rate is crucial for several reasons: When orders are fulfilled accurately, customers receive the correct products in the right quantities and specifications, leading to a positive experience and building trust and loyalty.
Order accuracy rate also reflect the effectiveness of various supply chain processes, such as order processing, inventory management and picking and packing. A high rate indicates that these processes are well-designed and executed, minimizing errors and ensuring the right products are shipped to customers. Additionally, a high order accuracy rate contributes to lower operational costs. When orders are fulfilled accurately, there are fewer returns, replacements or customer complaints. This reduces inefficiencies from rework, extra shipping costs, fixing mistakes and managing customer complaints.
If you monitor and improve your order accuracy rate, you can better identify areas for improvement. These could include actions like:
- Enhancing quality control measures
- Providing proper training to staff
- Implementing technology solutions like new software or automation
Order accuracy rate is a reliable metric for evaluating supply chain quality and driving continuous improvement.
Tips for effective supply chain performance measurement
Now that you know some of the essential supply chain KPIs, it’s time to learn practical tips to measure supply chain performance. If you’re using a contract logistics or third-party logistics (3PL) provider instead of fulfilling orders in-house, ask your 3PL provider for access or guidance to obtain any needed data.
1.Define clear and relevant KPIs aligned with business objectives
To effectively measure supply chain performance, begin by establishing clear and relevant key performance indicators (KPIs) that align with overarching business objectives. These KPIs should provide visibility into various aspects of the supply chain, tailored to specific goals. For instance, if enhancing delivery speed is a priority, metrics like on-time delivery, on-time supply and lead time are pertinent. Similarly, for businesses focusing on optimizing inventory management, metrics such as inventory turnover and days of supply offer valuable insights.
It's crucial to select KPIs that are both measurable and meaningful, directly contributing to desired outcomes. Each KPI should be clearly defined, with associated targets for performance. Regularly evaluate and refine chosen metrics to ensure ongoing relevance and effectiveness in gauging supply chain performance.
2.Establish data collection and reporting mechanisms
To ensure effective measurement of your supply chain network's performance, it's crucial to establish robust data collection and reporting mechanisms. Implement advanced systems and processes across various touchpoints within the supply chain to gather accurate and timely data, covering aspects such as order fulfillment, inventory levels, transportation, warehousing and customer satisfaction. Enhance efficiency by leveraging technology-driven fulfillment solutions that automate data collection processes and minimize manual errors.
Following this, create a centralized database or platform to organize and store the collected data, facilitating easy access and analysis for meaningful performance measurement. Develop tailored reporting mechanisms to track and analyze the data, utilizing customized dashboards, reports or visualizations to gain insights into key supply chain performance metrics and trends. Lastly, ensure data accuracy and integrity through periodic audits and validation processes, continually reviewing and refining data collection and reporting mechanisms to adapt to evolving business needs and changing market dynamics.
3.Regularly monitor and analyze performance data
Regularly monitoring and analyzing performance data is essential for an effective supply chain strategy. Establish a consistent schedule for data analysis, whether it's daily, weekly or monthly, tailored to your business's needs and the metrics being assessed, enabling timely identification of trends, issues and areas for improvement. Utilize technology and software tools to streamline data analysis, consolidating data from multiple sources, automating calculations and generating visual reports for enhanced understanding.
When analyzing performance data, contextualize it within your supply chain strategy and objectives, identifying patterns, trends and anomalies that may indicate potential risks. Compare current performance against historical data and industry benchmarks to evaluate the effectiveness of your supply chain operations. Use insights from the data analysis to pinpoint areas requiring action and involve relevant teams or departments in the problem-solving process to drive continuous improvement.
4.Benchmark against industry standards and best practices
Benchmarking against industry standards and best practices is essential for evaluating your supply chain performance and identifying areas for enhancement. Begin by conducting thorough research to identify relevant industry standards and best practices pertaining to key supply chain processes, encompassing metrics such as order cycle time, inventory turnover and customer satisfaction ratings. Collect data on your supply chain performance and compare it against industry benchmarks to identify gaps and areas requiring improvement. Industry benchmarks can be obtained from reputable market research firms like Gartner and SCORmark, or from your 3PL provider, if applicable. Ensure to regularly review and update your benchmarking efforts to stay aligned with evolving industry standards and best practices. By continuously benchmarking your performance against industry peers, you can stay competitive and drive ongoing improvements in your supply chain operations.
5.Leverage technology for supply chain performance measurement
Effective measurement of supply chain performance is paramount for businesses striving to boost efficiency, cut costs and elevate the post-purchase customer experience. To harness the complete potential of your supply chain, leverage technology-driven solutions such as automated data collection, sophisticated analytics and real-time visibility tools. By embracing these advanced capabilities, you can attain precise measurements and key performance indicators (KPIs) essential for optimizing your supply chain operations.
6. Implement predictive analytics for proactive decision-making
Consider incorporating predictive analytics into your supply chain performance measurement strategy. By leveraging historical data and advanced algorithms, predictive analytics can forecast future trends, demand patterns and potential disruptions in your supply chain. This proactive approach allows you to anticipate challenges and opportunities, enabling timely adjustments to inventory levels, production schedules and distribution strategies. By staying ahead of the curve, you can minimize risks, optimize resources and enhance overall supply chain efficiency.
7. Conduct regular cross-functional collaboration sessions
Facilitate cross-functional collaboration sessions involving key stakeholders from various departments, including logistics, procurement, sales and customer service. These collaborative meetings provide an opportunity to align on supply chain goals, review performance metrics and identify improvement opportunities collectively. Encourage open communication, brainstorming and knowledge sharing to foster a culture of continuous improvement and innovation within the organization. By bringing together diverse perspectives and expertise, you can gain valuable insights, drive consensus on performance priorities and implement targeted initiatives to enhance supply chain performance.
How a 3PL can help you measure and optimize your supply chain performance
Partnering with a third-party logistics (3PL) provider offers numerous benefits for measuring and optimizing supply chain performance. 3PLs possess advanced data analytics capabilities that enable comprehensive tracking and analysis of key performance indicators (KPIs) across the supply chain. Additionally, their expertise in logistics and supply chain management allows for the identification of inefficiencies and areas for improvement. By leveraging their technology-driven solutions and industry insights, businesses can gain real-time visibility into their operations and make data-driven decisions to optimize processes and reduce costs.
3PLs often offer scalable solutions, allowing businesses to adapt to changing demand patterns and scale operations efficiently. Ultimately, partnering with a 3PL provides access to specialized expertise and resources, empowering businesses to enhance overall supply chain performance and drive competitive advantage in the marketplace. Take the first step toward a more efficient supply chain by reaching out to Cart.com today.
About the Author
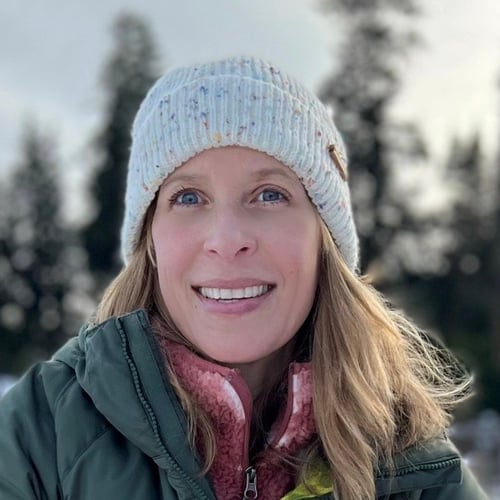
Alyssa Wolfe
Alyssa, a seasoned Digital Marketing Specialist with over 14 years of expertise, excels in project management, strategic development, and content creation. With a proven track record in crafting and executing successful online campaigns, she brings a wealth of knowledge in SEO, social media strategy, and data analytics.
Read Full BioSubscribe to our emails for the latest industry insights!
By entering your email, you agree to receive marketing emails from Cart.com